The Monarch Cosplay – Chest Armor
The Monarch’s Chest Armor is the defining piece of his costume; the Piece De Resistance. Or whatever. It’s the biggest piece to make (literally), the most challenging, and ultimately the single most important/obvious one.
Our Chest Armor is made of Wonderflex (WF). Making the Armor out of WF allows you to make it one large piece, with a single seam up the back – no complicated fasteners needed. The process involves making a fitting assistant or Clone of yourself, “sculpting” the armor Form on top of that, then curving the WF over your Form to create the finished piece.
WF is easiest to work with when you have something to shape it ON. You can work it by hand, but that gets tedious. The easiest way to do this for armor is to start with a torso. You could use a mannequin, or cast your body in plaster. Or you can easily and cheaply make a copy of your own by Cloning Yourself using duct tape and stuffing/batting. Just follow the instructions there – all you need is some tape and a henchman.
Once you have your Clone, sturdy him up a bit. We layered some fiberglass and resin on our Clone to make him more rigid, so he’d stand up to the constant maneuvering and abuse he was about to undergo, then painted the whole mess because we like black. Remember: Layering WF requires both heat and pressure, so you’ll be applying decent force to this thing. You don’t need to reinforce it, but it helps when shaping the WF, and will make your Clone last longer – focus especially on the upper neck/shoulders, and the chest. Don’t make the sleeves too long or stiff, since you’ll have to get the armor around them to get it off the Form later – just long enough to see where things should go. NOTE: Our first Clone got warped/smushed making our first set of Armor – the shoulders and neck were too fat to be useful and we recycled it into this one.
Now it’s time to make your Armor Form. You’re going to “sculpt” the shape of your Armor right on top of the Clone you just made – that way you know it will fit. The first time we did this, we used only cardboard, thinking we could smooth out the WF by hand later on. NOTE: This was a mistake – it is difficult and very time-consuming to change a small portion of a piece like this without altering everything around it. The second time we started with cardboard, and finished with a layer of Bondo Body Filler.
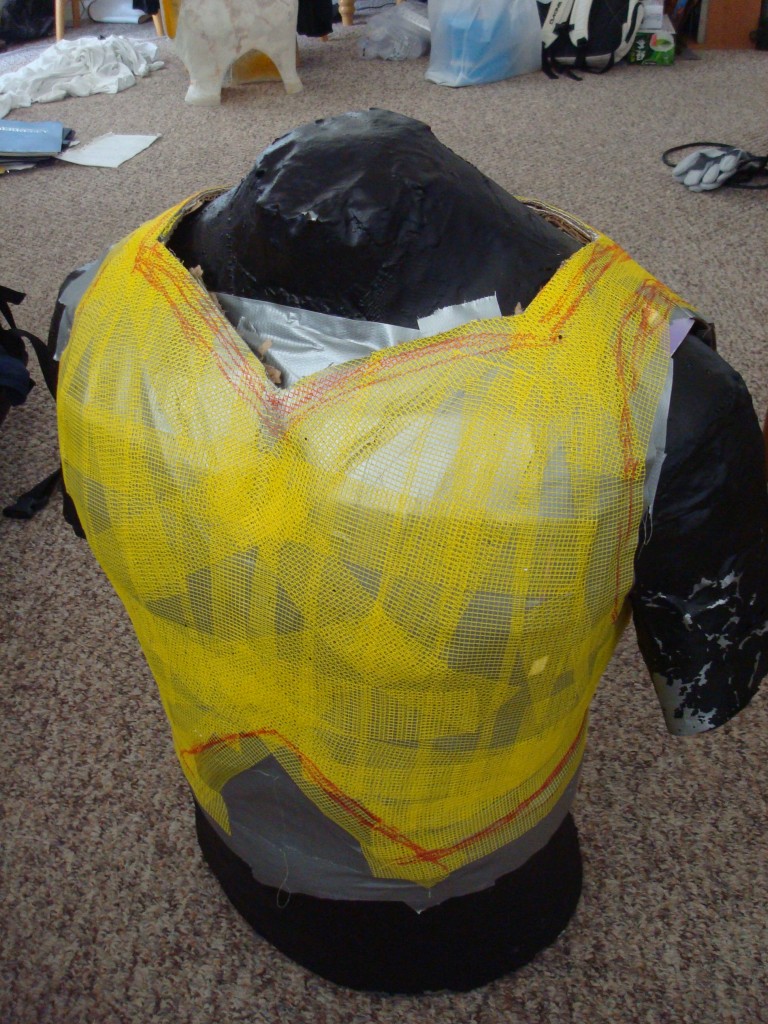
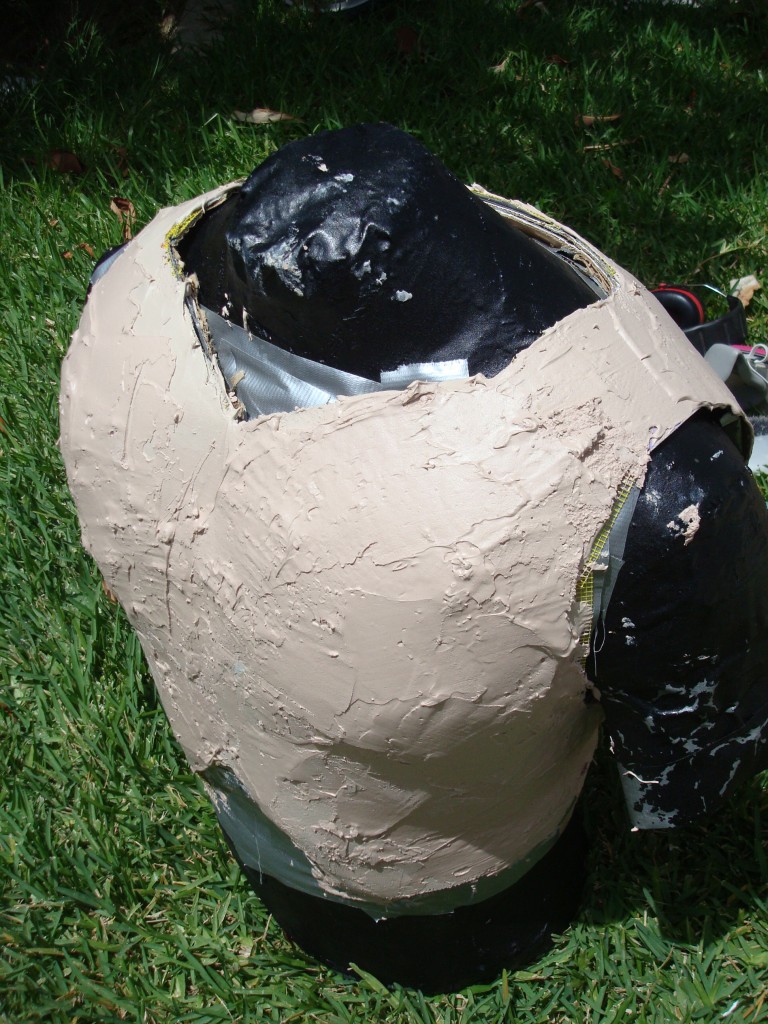

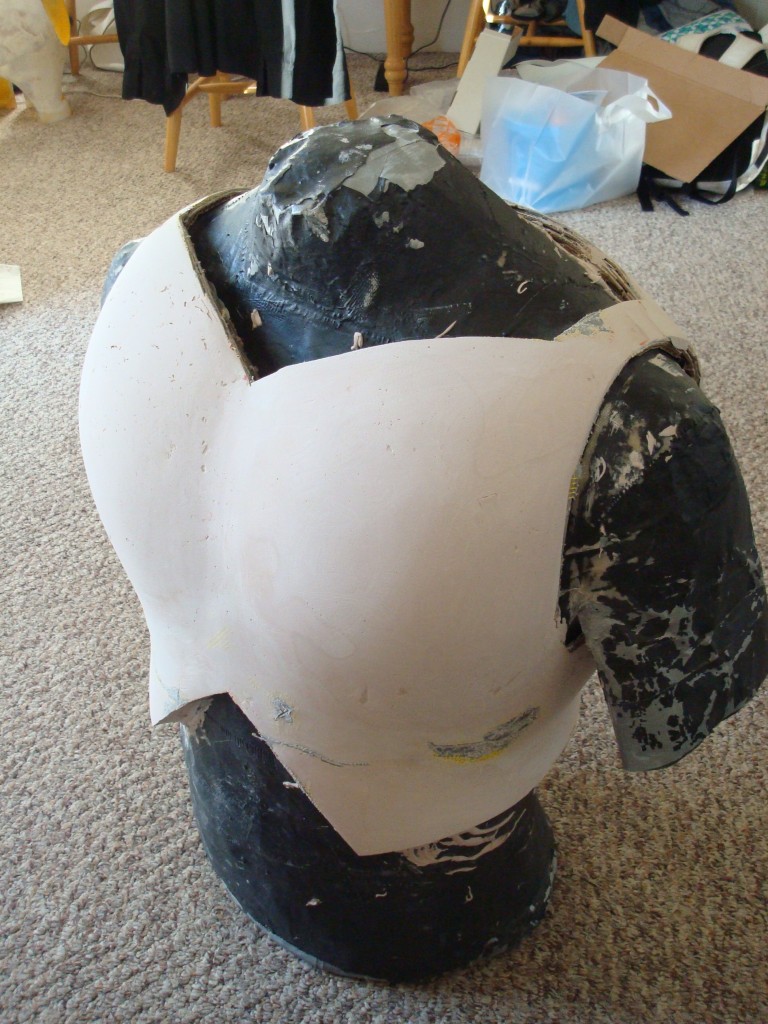
Start with cardboard for your basic shape. NOTE: If you want to make it easier to remove the Form from your Clone when you’re done, wrap the Clone in paper or plastic wrap first. Then go crazy with the cardboard and tape. Masking tape is perfect because it’s cheap, flexible, and you can cut/sand through it with ease if you need to later. Remember: You’ll want a decent amount of space inside the armor so you can move – things like bending and twisting your torso are painful/impossible with armor that’s too tight, so put some thickness in those first layers. Keep in mind what the final shape will be, but don’t hesitate to slap cardboard wherever you need it to make the shape look right. NOTE: Use tape to cover edges and gaps between cardboard pieces – the less space you have to fill with Bondo the better. We also used fiberglass drywall-joint tape to make the Bondo stick better – this is strictly optional.
When you think you’re close to the shape you want, draw the final outline directly on your cardboard Form. Cut off any extra cardboard with a box cutter, making sure to reattach anything that comes loose. NOTE: We did not do this, and we were forced to go back after starting with the WF and cut clean edges so we could properly shape our Armor.
At this point you should have a rough cardboard version of what your Armor will look like. It should be slightly smaller than you want the final piece to be, because you are about to slather it with Bondo. NOTE:Gauging exactly how much cardboard versus Bondo to use is tricky. Ideally you’ll use just enough Bondo to smooth everything over and create the elegant, complex curves you want. In practice this rarely happens. You will almost certainly have areas with too much cardboard, and areas with too little.
Although you will need a lot of Bondo (we used nearly a gallon), work in small batches. Remember: Bondo hardens faster with sunlight and heat, so work away from both. We recommend using the actual Bondo/3M brand spreaders you’ll find wherever you buy your Bondo – they’re flexible, and make curves easier than rigid spreaders will. NOTE: Don’t try to get everything perfect with the first layer. As we said, it’s likely you’ll have some areas that need more work than others. Get a solid coating of Bondo on everything first, then go back and add more where you need it.
Once the Bondo looks good, it’s time for sanding! You really, really want a power sander. Even if it’s a crappy square sander from a swap meet or garage sale, get one. Start with some really heavy 60 grit sandpaper. Depending on the shape of your Armor, and how smooth you made your Bondo, you might want to start with a heavy-duty rasp/file. Go crazy – shape the Bondo down to where you want it, using whatever tools are easiest. We used a combination of heavy rasp, Dremel, square and random-orbital sanders.
When you have the shape almost perfect, switch to a higher grit sandpaper, like 220. The Bondo doesn’t have to be paint-grade smooth, but the WF will pick up a surprising amount of detail when you heat it up as much as you’re about to do.
You might sand through the Bondo and expose your cardboard, but still want to carve the Form down farther. Just cut out the exposed cardboard, plus a healthy chunk of the area around it, with a box cutter. Then put more Bondo in the gap you made and continue sanding. If you find areas/gaps that should stick out more, just add more Bondo (and/or cardboard) and keep sanding. You can repeat this process infinitely, or until you’re satisfied with the results.
When you’re happy with the Form, it’s time for the WF. NOTE: If there is any exposed cardboard or tape, cover the Form with tin foil. WF gets very sticky when hot, and though it will peel off Bondo fairly easy it won’t come off cardboard or paper (like masking tape). Tin foil peels right off, as does plastic wrap – but plastic wrap can’t withstand the heat. We recommend clearly marking things like center lines before you get started – it makes it easier to get things symmetrical later.
WF now comes with a “smooth” side and a textured side. It sticks to itself regardless of which side you use. Make the armor two layers thick – it will be sturdier and hold its shape better. We recommend putting the smooth side in for the inner layer, and out for the outerlayer. This will make it easy to paint, and leave fewer rough edges to snag clothing/skin on.
Start with a great big piece of WF for the first part. You can make a rough pattern using paper if you like. Remember: WF stretches in proportion to its size, so big piece will stretch a lot. Start from the front – you want the front to be the smoothest and most polished looking. Work your way around, stretching, smoothing, and pressing the WF onto your Form. Cut and trim as needed to make things lay smoothly. Tack edges down with masking tape if it moves too much. With patience and effort, you can make the WF exactly match your Form.
After the front piece is done, do the same from the back, overlapping the pieces when you get to the sides. Trim the edges of both halves before overlapping – this will create cleaner lines later on, and make any extra smoothing easier. When starting with a new piece of WF, start forming either from the center (if it’s a new section), or from the edge you’re overlapping (if continuing from an adjacent piece). If you don’t, you may end up with wrinkles at the overlap if you have to stretch the WF further. NOTE: Wrinkles are a pain to fix, are ugly, and create extra-stiff areas – usually where you don’t want them; avoid them.
Continue like this, adding new pieces of WF until the whole Form is covered. Add extra layers in high-stress areas like the shoulders and the center of the chest. Remember: WF will bond to itself when hot – if both layers are hot enough they fuse into one solid layer. Reinforce any spots that seem weak, or where you cut sharp corners – like the front “V” shapes. We recommend trimming and rolling/folding the edges under – it adds another layer of stability, and creates a nice smooth appearance. We shaped the front edges to be almost triangular, making the armor look much thicker than it actually is.
NOTE: WF will pick up enough detail from sub-layers that edges will show through to the top layer – be careful when layering. To hide/smooth any lines from hidden layers/edges, get the area good and hot and roll over it with something like a pen – a sharpie works well because of its slightly curved shape.
NOTE: WF normally retains heat, and Bondo acts like an insulator – it’s convenient to have a fan handy to cool off the areas your working on as you hold them in place. The most time-consuming aspect of using WF, especially on a large piece like the Armor, is waiting for one section to cool so you can move onto the next one.
When all the WF is done and completely cool, it’s time to take it off your Form. Find the center line on the back of the piece – this is where you’ll cut. NOTE: This is one place where it’s especially important to double-check everything. Cut completely through all the layers of WF from the collar to the bottom edge. Double check that the layers here are completely bonded to each other – you don’t want them to separate when you attach the fasteners.
Now comes the moment of truth! Peel the WF off your Form. It will stick, so proceed slowly. A flexible putty/spackle knife may be helpful to pry loose any especially stubborn parts.Remember: WF loses its flexibility if it’s especially thick – places like the shoulders can actually crack/break if you’re not careful. NOTE: If anything breaks, don’t worry – enough heat and pressure and the edges will melt right back together, and some WF scraps underneath will ensure the area is solid.
When the whole piece is loose, it should come right off the form – some bending and contorting may be required. When it does, congratulations! You now have a piece of armor that will fit you perfectly. Go ahead and try it on to be sure, but have a henchman handy – getting back out can be tricky.
The next stage is painting. You’ll prime your everything first. Use a flexible automotive High Build primer, coupled with a flexible Adhesion Promoter. Bulldog makes both, and they’re commonly available at auto supply stores. The Adhesion Promoter ensures the primer bonds with the plastic of the WF and can flex/bend adequately, and the High Build primer will make it easy to get the Armor looking glossy-smooth. There are cheaper High Build primers (Home Depot sometimes carries a Rustoleum version), but they don’t have the flexibility and bonding strength of good auto primers. Remember: The quality of your primer is what determines how well the surface coat sticks to your final piece.
Coat everything with primer, including any parts of the inside which can be seen through arm holes, from underneath, etc. We painted everything to be safe. At this point, check that everything is smooth, with no visible seams/lines – edges and overlapping pieces are prime locations. Any areas that need work can be further smoothed with a thin layer of Bondo.NOTE: It is easier to see imperfections after everything is primed the same uniform color, which is why you’re doing this now. When it looks OK, apply more primer until you have enough paint to sand everything smooth. Once the primer dries, sand it lightly until it feels sleek – start with 120 grit, then move on to 220, and finish with 300.
Dust/clean everything thoroughly, then paint it. There is a sparse selection of yellow aerosol paint – Rustoleum and Krylon each make 2 colors. Montana Gold (available at Blick and other art stores) comes in about a dozen shades, but is only available in matte finish. We used Krylon gloss yellow. It goes on very, very thin, but dries to the touch and is repaintable in about 10 minutes. Be patient, and expect to use several cans (we used 3). It will take many coats to get a consistent, solid yellow, but the finish is very smooth and durable.
Once all the paint is fully cured it’s safe to move on to attaching fasteners and harness. Our armor uses a separating zipper to close the back seam, but you can also use velcro or something similar. NOTE: Make it simple – someone else will be strapping you into your armor. Barge Cement (available at hardware and craft stores) works excellently, and will bond to anything you use here.
Unless it is secured to your body, the Armor will ride up to you neck. To keep it in place, we snap it to an elastic harness straps around the chest. We started with a set of hockey pads found at a second-hand sporting goods store, cut off all the plastic and extraneous bits, and sewed heavy-duty snaps to the shoulder/neck portion. Then we used Barge to attach the other half of the snaps to the underside of the armor. You could create a similar setup from scratch using elastic and velcro. NOTE: Double check that everything lines up correctly before attaching anything – your Clone will be useful here.
The shoulder pads are made of WF, following the same method used for the Armor. Except instead of using cardboard we used expanding foam insulation (comes in a can at hardware stores), which we carved with a serrated knife, then covered with Bondo. It was easier making the curve of the shoulders this way than cardboard would be. They are attached directly to the Armor with a piece of yellow fabric – in our case scraps from our boots, so it matches everything else. The wings are secured with a single strip of velcro, glued on with Barge. You can make the Monarch logo with vinyl decal material from craft stores, though we had ours professionally printed from an Adobe Illustrator image we drew. In fact, you can ask Jennifer Allman to print one up for you, too – she has them ready to order.
That’s it, your Armor is done! Now get suited up and go show the world just how malevolent you truly are!
Written by Steven Meissner, SoloRoboto Industries
Discuss this story in our Venture Forums! Follow @VentureBrosBlog on Twitter and be sure to “LIKE” us onFacebook for the latest Venture Bros. news!
[Venture Bros. Blog]